Liquid Loss-in-Weight Feeder
Company Profile
NANJING PEGE TECHNO MACHINE CO., LTD is a leading quality and customer-oriented manufacturer, specialized in providing various machines for rubber and plastic industry. Rubber sector machines focus on deburring and cutting include cryogenic de-flashing machine, spin trim de-flashing machine as well as rubber strip or gasket cutting machine. Plastic sector machines focus on material precision feeding and mixing including Gravimetric Loss-in-weight (LIW) feeders and its affiliated system including uploading and supplementary system.
Our plastic machine department also continuously develops and optimizes the Gravimetric loss-in-weight feeding machine to meet the customer demand to improve feeding efficiency, to reduce labor work tense as well labor cost.
Gravimetric Feeder is widely applied in the industry of Plastic, Chemistry, Food and Pharm, used for material precision mixing, dosing, and feeding application.
By using world well-known brand components and high professional production technology, all the machines produced by NANJING PEGE company are of reliable quality and high stability with the features of lower energy consumption as well as less maintenance cost. With the efforts from our sales and production team, the "Frozen Shot" brand PG series cryogenic deburring machines, ‘PG’ brand Gravimetric LIW Feeders are sold not only in the domestic China market, but also many other countries like Poland, Russia, Croatia, Slovenia, Hungary, Malaysia, and more from all over the world.
Working Principle
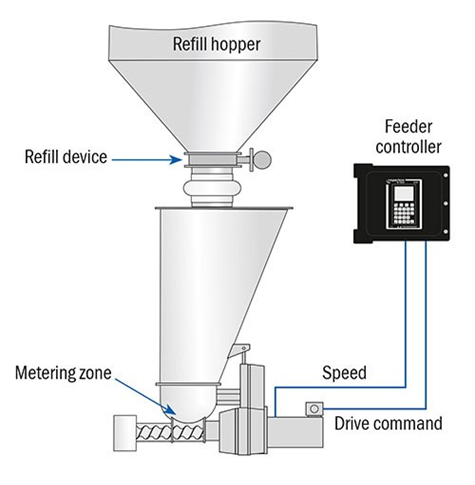
The measuring hopper is mounted on a platform scale (frame structure equipped with precision sensors). When the feeder is running, the motor drives the feeding screw, vibrator or pump to move. At the same time, the material in the measuring hopper flows out. By reducing the weight in the unit time, obtain the actual feeding amount, compare it with the set feeding amount to get the error value, and then adjust the speed of the feeding motor through the PID closed-loop control algorithm to achieve the precise feeding requirements. This process ensures an accurate feeding or dosing during the production process. The general purpose of Loss in Weight feed system is to accurately weigh and control the output of variable products either, continuously or as a batch.
Benefits of Loss-in-weight Feeder
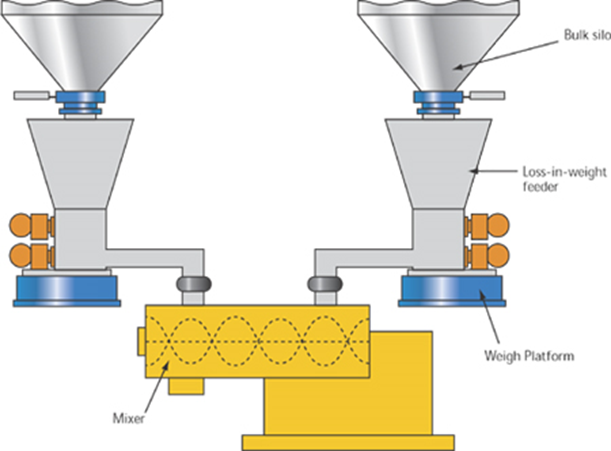
Typical loss–in-weight feeders are used to negate the use of weigh hoppers and to eliminate the impact of material. This system is particularly useful when the product to be weighed is sticky and does not have good flow properties.
A. Improve measurement accuracy
B. Reduce premixing workload
C. Improve product stability
D. Reduce dust pollution and be more environmentally friendly.
E. Improve work and production efficiency.
Applications on the Industries
The key function of loss-weight-feeder is to realize continuous and precise batching and dosing.
Plastics industry.
Processing of plastic, films, coatings.
Chemical industry.
Premixes for extrusion, detergents, pesticides, fertilizers, building materials.
Food Industry.
Cereals, muesli bars, sugar mixtures, milk powder, diet breakfast drinks, salt iodization, fluoridation, aromatization.
Pharmaceutical industry.
Production of vitamins and active ingredients.
Environment.
Flue gas cleaning, water processing, diesel particle filters.
Features of Liquid Loss in Weight Feeder
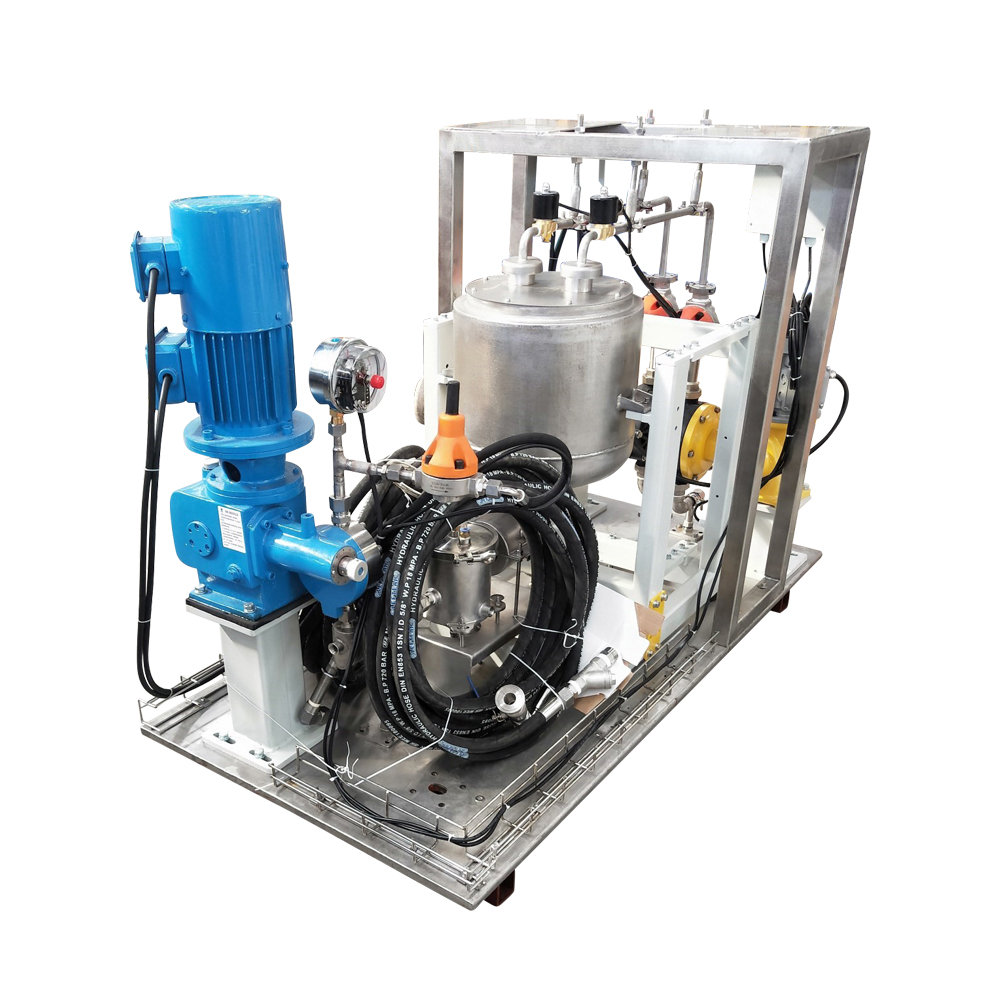
★ The cantilever sling type weighing frame supports the storage hopper, which has the characteristics of vibration reduction and anti-level interference, which can effectively shield the non-weight value interference from the vibrator, and measure the flow of the system more accurately.
★ Stainless Steel bellow sensor has the feature of only slight deformation after long time use, and high precision with less signal drift, and is durable for bad environment use.
★ 485 Digital transmission of weighing data has the feature of no attenuation and anti-interference during the period of data transmission.
★ Hydraulic Diaphragm Pump, Plunger Pump, Gear Pump are selectable.
★ Equipped with complete isolated SUS304 bellow spring damping type spray gun, has the feature of keeping pressure stable within 24 hours.
Explosion proof, heat preservation by water or electricity are
Sucessful Cases of Pege's Weighing Dosing&Batching System
With many years of expertise and continious development, the gravimetric feeding machines had been accepted by many customers and are applied in many industries.
Pege will keep providing qualified loss in weight weighing feeder for customers both in China and Abroad.
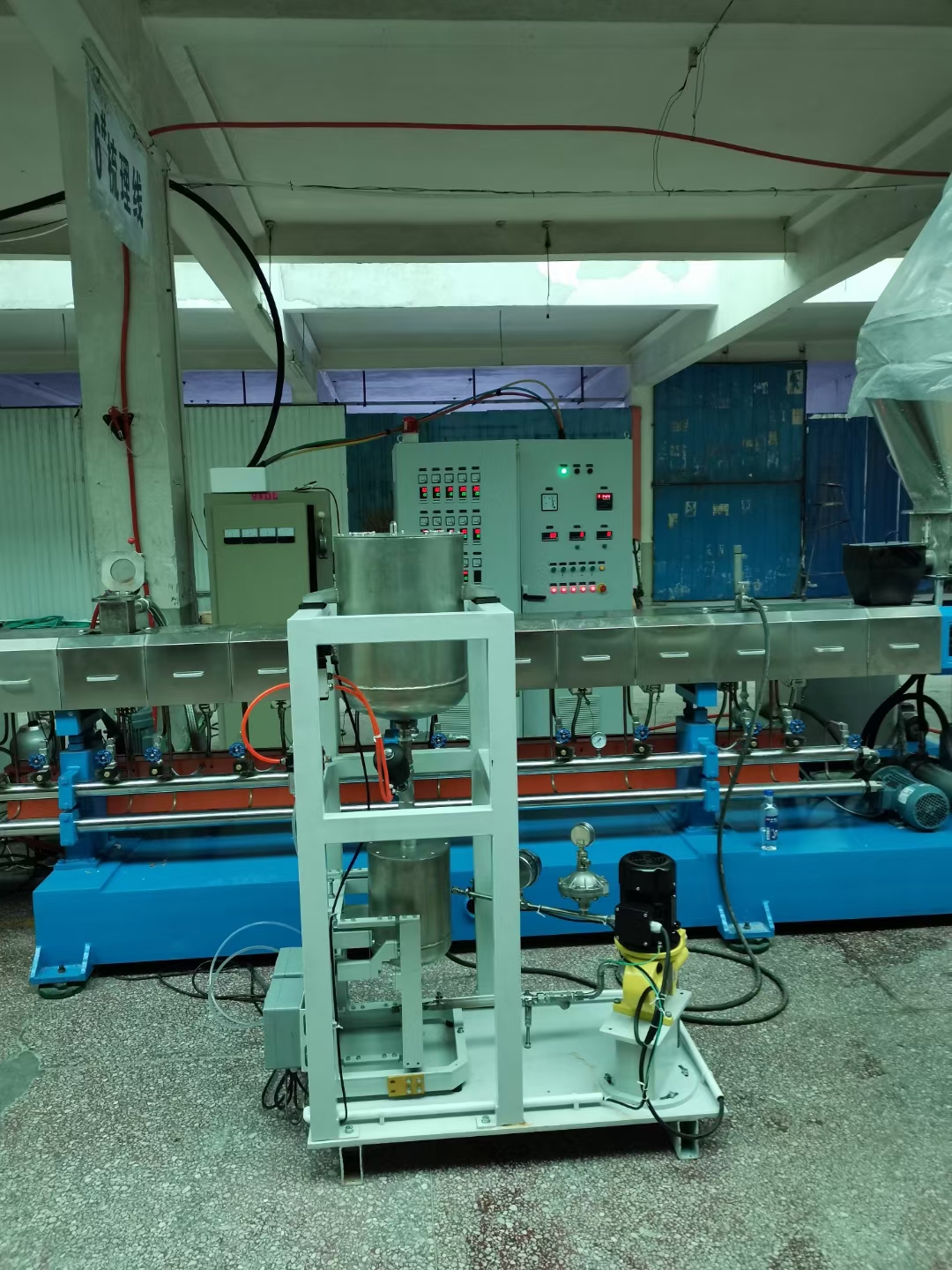
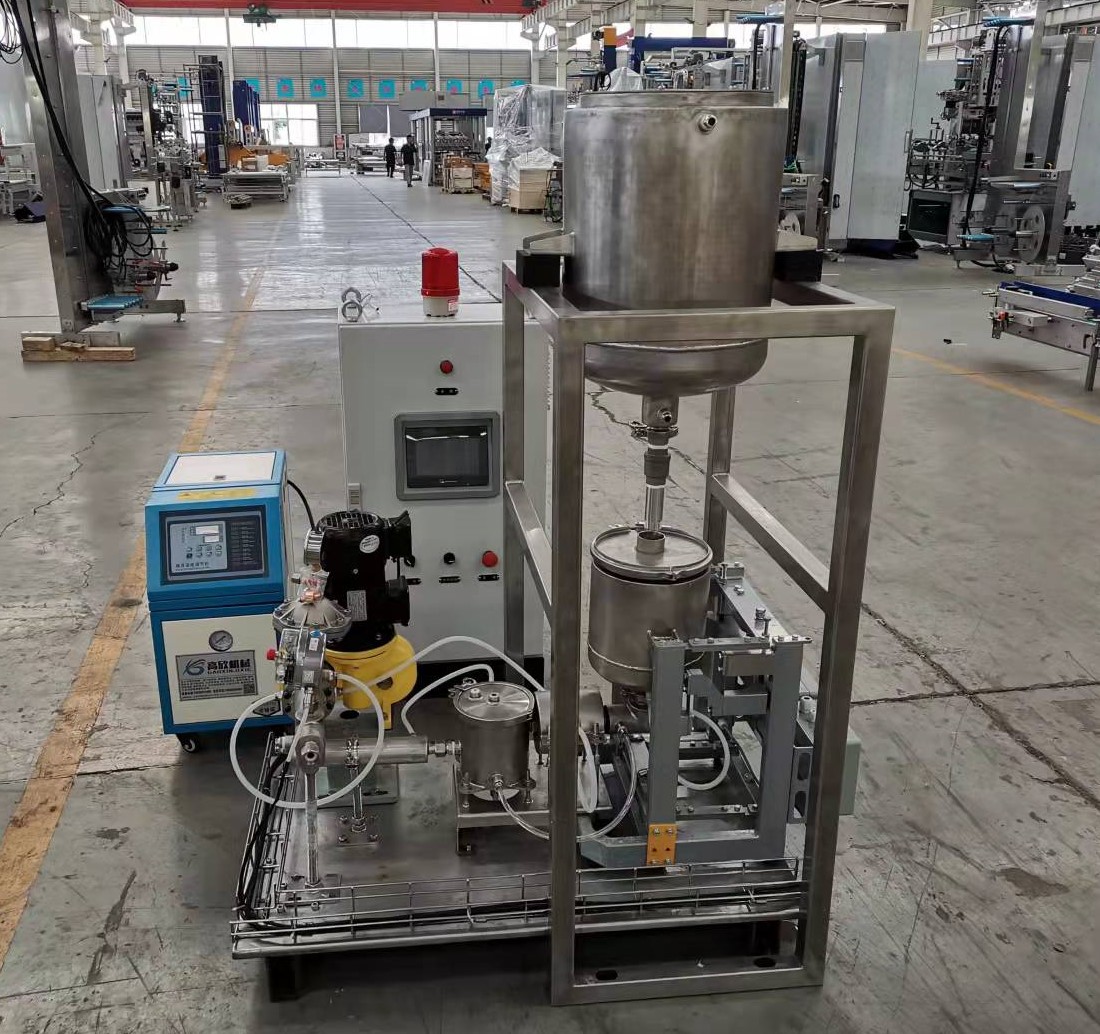
FAQs of Loss in weight Feeder
1. How does weighing feeder work?
Gravimetric loss in weight feeder is an instrument that is important to control and measure the speed of a substance in an instrument system. This equipment can handle the bulk solids. It allows the solid to discharge at a constant weight per unit time. The unit of measurement is kg/min or Kg/hour. The signal about the weight is used as a system of feedback control. It controls and monitors the feed rate that enters a instrument. The weighing systems include several examples such as platform scales, load-cells, weigh hoppers, etc. Depending on the overall process, the gravimetric feeder may be a loss-in-weight system or a gain-in-weight system.
2. What are the most important benefits the gravimetric feeder can give to you?
To ensure excellent quality of final product by accurately metering the bulk ingredients.
To reduce the labor cost and improve labor work environment
To Improve product stability
Reduce dust pollution and be more environmentally friendly
3. What is general accuracy rate of the good loss in weight feeder?
Our general feeder’s feeding accuracy rate can be 0.5%. The micro twin screw loss in weight feeder accuracy rate can be up to 0.3%.
4. What is the main composition of a typical loss in weight feeder?
Loss-in weight feeders for bulk materials consist of storage hopper, controlled feeding devices such as augers, screws chutes, pumps as well as scales or load cells, loss-in-weight controllers or rather loss-in-weight feeder controllers. Optional: e.g. agitators to improve the quality of the bulk material.